Manufacturing automation is broken.
We add the intelligence to fix it.
Intelligent automation that works like a human, scales like a machine. No more expensive setup. No more rigid systems.
No setup required • See it work in 2 minutes
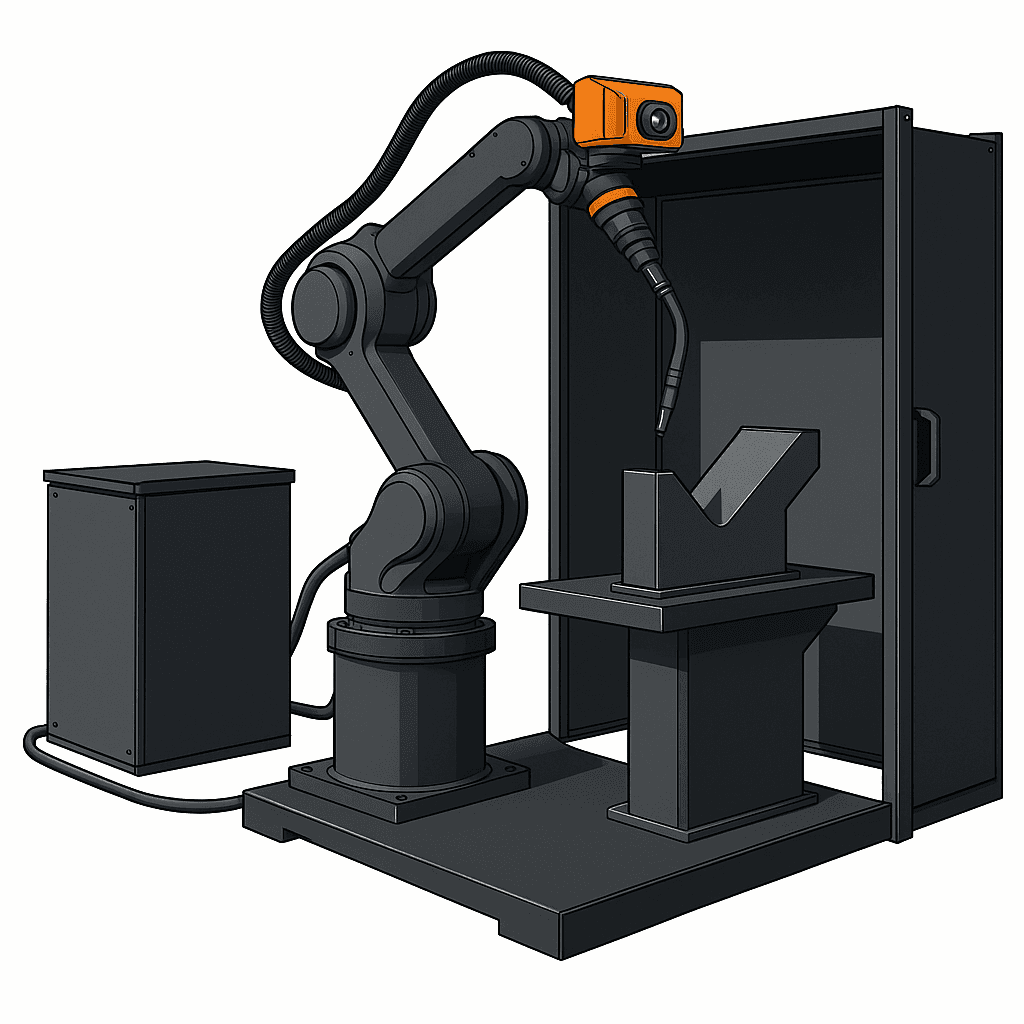
The Problems We Solve
Traditional automation is too rigid, too expensive, and too complex for modern manufacturing.
Robots Are Blind
Traditional robots are like expensive calculators - they can only do exactly what you program them to do, and they break when anything changes.
Our Solution:
Our robots can see, think, and adapt like a human worker - they handle variations and changes automatically.
Automation Setup Is Fragmented
Setting up traditional automation is like building a custom house - it takes months, costs a fortune, and you can't change anything once it's built.
Our Solution:
Our system works like a smartphone app - you turn it on and it just works.
Manufacturing Is Facing Labour Shortage
Skilled welders cost €125K/year and robot programmers are like unicorns - rare and expensive. The talent pipeline is broken.
Our Solution:
Our system eliminates the need for expensive specialists. Anyone can operate it.
How Our System Works
No more expensive setup. No more rigid systems. Just intelligent automation that adapts to your needs.
Scan Your Environment
Our AI-powered robot scans your workspace and identifies what needs to be done, just like a human would look around and assess the situation.
Simulate the Solution
Watch as our system plans and simulates the perfect approach, showing you exactly what it will do before it does it.
Automate Intelligently
The robot executes the task with human-like intelligence, adapting to changes and learning from each interaction.

See It In Action
Experience our intelligent automation system firsthand with our interactive showcase.
Ready to Transform Your Manufacturing?
Join the companies already using intelligent automation to reduce costs, increase flexibility, and solve the labor shortage.